Як роблять дріт?
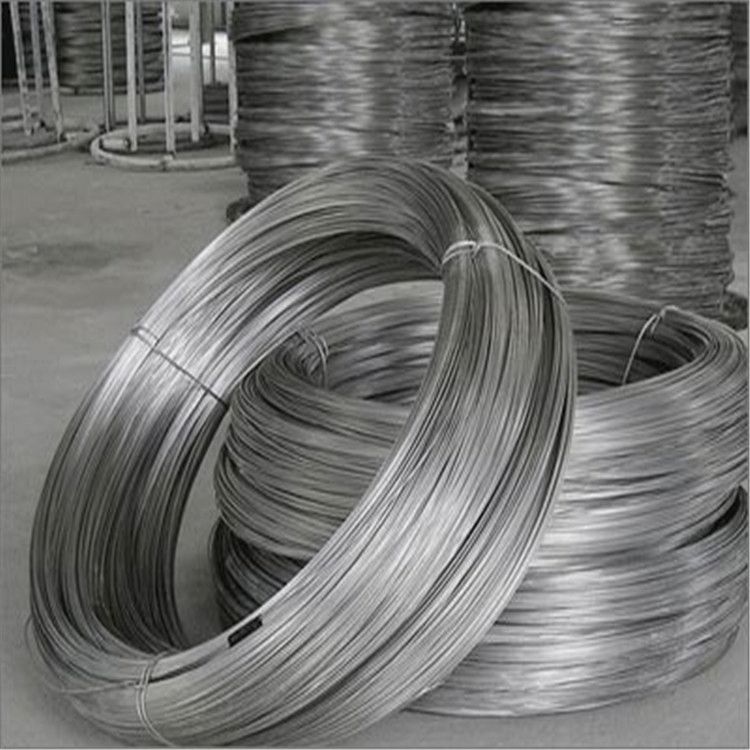
Дріт – це довга і, як правило, тонка кругла (рідше з трапецієподібним, квадратним або шестикутним перетином) нитка, створена зі сталі, міді, алюмінію (іноді з нікелю, титану, цинку, срібла та інших металів) або їх сплавів. Є також сучасна продукція, в основі якої – бі- або поліметал. Сировиною можуть служити і неметалеві матеріали.
Дріт легко згинається. Він дуже популярний і використовується в найрізноманітніших царинах життєдіяльності. Він важливий у промисловості і користується неймовірним попитом у побуті. Сфера застосування залежить не в останню чергу від товщини. З нього виготовляють електропроводку, металовироби, пружини, свердла, термоелектричні перетворювачі, електроди, електронні пристрої та ін. Колючий дріт приходить на допомогу, коли потрібно обгородити загін для худоби або спеціальний об’єкт з обмеженим доступом. Завдяки значній міцності не є винятком використання дроту для підтримки мостів та інших споруд. Навіть творчі люди часто задіюють його при декоруванні, в облаштуванні інтер’єру і виготовленні прикрас, створюючи як окремі деталі, так і цілі оригінальні композиції (сережки, підвіски, світильники, стільці, картини, годинники, фоторамки та багато іншого).
Різновиди дроту
Передусім, він поділяється на види за матеріалом виготовлення (основні з них перераховані вище). Від матеріалу залежать характеристики продукту. Найдоступніший в плані вартості – сталь, зазвичай потребує покриття цинковим або алюмінієвим шаром-захистом, що запобігає окисленню на повітрі. Не виняток – обміднення сталі, хоча і власне мідний дріт часто незамінний.
Крім того, існує поділ за розміром (діаметром). Варіативність у цьому плані – дуже велика: від декількох десятих міліметра до десятків мм. Також за основу може братися площа поперечного перерізу (електрична провідність), музична нота, що отримується в конкретних умовах і число проходів через волоку при виробництві.
Особливості виробничого процесу
Раніше дротовиробництво виглядало так: працівник розігрівав шматок металу, проштовхував його через отвір у шаблоні з металу, закріпленому на верстаті. Далі необхідно було схопити кінець, який з’являвся, і витягнути його з отвору. Всі процеси виконувалися вручну, а товщина виробу залежала безпосередньо від сили, що прикладалася людиною.
Сьогодні, звичайно ж, всі етапи автоматизовані. Але суть – та сама: дріт протягують або волочать крізь поступово зменшувані отвори. Перед цим бруски металу нагрівають (здійснюють термообробку) і готують до волочіння. Розплавлена маса надходить на колеса-проштовхувачі, а на виході отримуються ті ж, але більш досконалі довгі смуги. Їх намотують на котушку або надають товару форму мотка, адже так зручніше і перевозити, і зберігати виріб.
Основні операції можуть повторюватися кілька разів. Все залежить від потрібного діаметру.
Інші важливі процеси:
- травлення в розчині H2SO4 або за допомогою іншого травителя (для вилучення оксидів і нальоту);
- нанесення покриттів (для надання спеціальних властивостей);
- гартування в печі (для зменшення ламкості і забезпечення однорідності механічних властивостей по всій довжині).
На замітку! Щоб уникнути пошкоджень поверхні дроту, робочі ділянки волочильного стану потрібно покрити змазкою.
Устаткування
У роботі можуть використовуватися стани мокрого або сухого волочіння.
В основі роботи перших – технології ковзання. Вони сумісні з різнократними станами сухого волочіння. Можуть бути обладнані різними модифікаціями електричних двигунів.
Що стосується других, то їх конструкція вдосконалена. Вони більш компактні, міцні та стійкі, позбавлені ременів і шківів, відрізняються безшумністю роботи і відсутністю вібрацій. Вони повністю підлягають транспортуванню, що зменшує витрати часу на монтаж і прокладку кабелів. Такі стани є найкращим варіантом для створення дроту з незначним діаметром з нержавійки, а також інших видів сталі (низько- і високовуглецевої).
Різновид станів сухого волочіння – прямоструменеві установки (барабани в них розташовуються горизонтально). Характеризуються значною надійністю, ергономічністю і простотою використання, відсутністю необхідності в спеціальному фундаменті для встановлення.
З-поміж іншого обладнання: печі, розмотувальні пристрої для катанки, крутильні машини бугельного, сигарного і двоскрутного типів.
Реактиви для покриття дроту
Щоб захистити дріт від різних впливів, на нього наносять покриття. Серед найпопулярніших – цинкове та мідне.
Цинкування та реактиви для нього
Гаряче цинкування – бездоганний спосіб захисту від корозії і механічних впливів. Щоб воно було виконано на найвищому рівні, необхідно здійснювати перелік підготовчих заходів: знежирення, травлення, промивання і флюсування.
Знежирення виконують із залученням лужних та кислотних розчинів. Яких саме – залежить від природи забруднень. Також реактиви потрібні на етапі травлення (зазвичай, це соляна кислота). Крім того, можуть бути використані піноутворювачі. Флюсова обробка передбачає застосування таких речовин, як хлорид амонію або хлорид цинку.
Якщо необхідно надати цинковому покриттю блиску й гладкості, варто задіяти обтиральні матеріали і спеціальні емульсії.
Міднення та використовувана хімія
Покритий шаром міді дріт – один з найбільш популярних у наш час. Для його створення залучають різні електроліти:
- кислі (сульфат міді + сірчана кислота);
- ціанисті (мідноціаниста комплексна сіль + ціанистий натрій + сегнетова сіль + натрій гідроксид);
- аміачні (сірчанокислий нікель, мідь, натрій і амоній + аміак);
- етилендиамінові (мідний купорос + сульфат натрію + сірчанокислий амоній + етилендиамін) і т.д.
Для знежирення можуть знадобитися: тринатрійфосфат, каустик, рідке скло, карбонат натрію. Для травлення: сульфатна кислота і хромовий ангідрид. Для сенсибілізації: хлорид олова і соляна кислота.
Склад розчину для тонкошарового хімічного міднення: сірчанокисла мідь, хлористий нікель, їдкий натр, вуглекислий натрій, тартрат натрію, формалін.
Склад розчину для товстошарового хімічного міднення: мідний купорос, каустична сода, вуглекислий натрій, гліцерин, формалін.
Міднення забезпечує добрий захист окремих ділянок сталевого дроту від навуглецювання, якщо далі передбачається різання.
Хімія для виробництва дроту
Дві головних сукупності хімічних речовин, які можуть знадобитися: очисна і мастильна хімія.
Для очищення. Найпопулярніші речовини для зняття окалини шляхом хімічного травлення – сірчана і соляна кислоти.
Сірчана кислота задіюється найчастіше для обробки сталевого дроту. Соляна кислота добре підходить для очищення дроту з міді і біметалічного. Часто ці два компоненти використовуються спільно.
Кислоти практично одночасно починають впливати і на метал, і на окалину, оскільки в останній є пори і тріщини. При їх впливі все зайве відділяється від виробу і переміщається в травильну ємність, де відбувається поступове відновлення воднем і розчинення в травильному розчині.
Результат залежить від температури і концентрації розчину. Мінімум часу знадобиться при концентрації 250-300 г/л. Якщо збільшити цей параметр, вплив сповільниться. Уповільнення процесу можна компенсувати підвищенням температури. Також збільшити швидкість можна перемішуванням барботажу, наприклад, за допомогою повітря, або погойдуванням металу, який обробляється. Це ще й позитивно позначиться на якості травлення.
Загалом, травлення в кислотах може тривати як кілька хвилин, так і годину, і більше, залежно від характеру окалини і умов травлення.
Для запобігання втратам металу і його псуванню можливе задіяння інгібіторів.
Інші речовини, які можуть застосовуватися при приготуванні розчинів для травлення: дихлоретан, ацетон, залізо хлорне і хлорид міді.
Для змащення
Речовини цієї групи безпосередньо впливають на якість зовнішньої поверхні виробів.
Важливі умови обробки:
- попереднє очищення від окалини;
- повне покриття поверхні змазкою;
- задіяння притискних роликів або цанг, які забезпечують належне прилягання змазки;
- наявність мастильного шару в будь-якому випадку, незалежно від високих температури і тиску.
Тільки так поверхня матиме бажану якість (висока стійкість до корозії, високоадгезія до різноманітних матеріалів), а процес відбуватиметься не надто довго.
Оптимальна кількість змащувальної речовини – 500-600 г на 1 тонну металу.
Основні компоненти, що використовуються для створення мастил: тальк, мило, церезин або віск. Активізатори: солідол, парафін. Хімія, що входить до складу: бура, сірка, вапно гашене, сульфат натрію, кухонна сіль.
З урахуванням усього сказаного вище можна зробити висновок: виробництво дроту – дуже важливий і необхідний бізнес, який, мабуть, завжди буде мати свого споживача. Щоб результати справи тішили вас щодня, подбайте про обладнання, реактиви для покриття і хімію загалом. Пам’ятайте, що наскільки якісною буде готова продукція, залежить від дотримання виробничих норм і вимог, а також від стабільності застосовуваної технології. Будуть запитання з приводу придбання хімічних матеріалів для створення дроту – звертайтеся!