Хімія для лиття металів
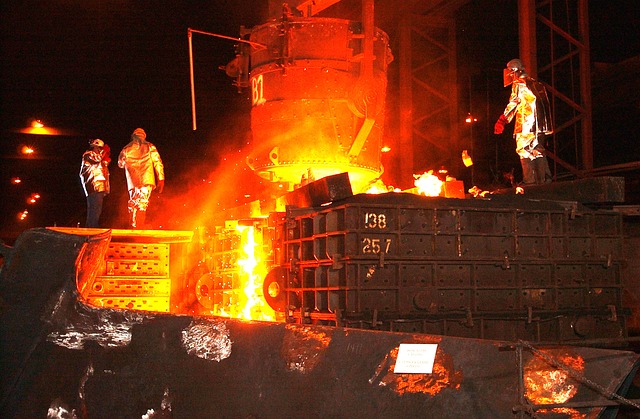
Лиття металів (ливарне виробництво) – надважливий напрям металургії та машинобудування, оснований на створенні фасонних заготовок/деталей способом поміщення металів у розплавленому стані у спеціальні форми, конструкції внутрішнього простору яких мають вигляд майбутнього виробу. Остудившись, метал, який був залитий, твердне, зберігаючи надалі конфігурацію необхідної порожнини, і отримує назву відливки. При цьому в процесі охолодження розплавленої сировини матеріал набуває важливих механічних та робочих властивостей.
Такий спосіб металообробки дозволяє створювати відливки різноманітних конструкцій. Вага може варіюватися від грамів до тонн, довжина – вимірюватися хоч в сантиметрах, хоч в метрах, товщина стінок – становити від 0,5 до 500 мм.
Які вироби можуть бути зроблені способом лиття? Найрізноманітніші: поршні і блоки циліндрів, колінчаті вали, корпусні елементи та кришки редукторів, шестерні, станини, турбінні лопаті й багато-багато іншого.
Які способи лиття існують? Їх також чимало, наприклад: у піщані/оболонкові/металеві форми, рідке штампування і лиття шляхом вичавлювання, по виплавлюваних моделях, шляхом вакуумного всмоктування і під низьким тиском, а також відцентрове, безперервне, електрошлакове та ін. На якому із способів найкраще зупинити вибір, залежить від низки факторів: від виробничих обсягів, вимог до точності геометрії та шорсткості поверхні, економічної вигоди тощо.
Типи металолиття
Ливарне виробництво може бути одиничним, серійним і масовим. Який би тип не був вибраний, процес все одно буде відзначатися трудомісткістю.
Для одиничного характерний випуск різних відливок в обмежених кількостях. Не є винятком те, що виготовлення цих деталей може бути в майбутньому повторене. Тут, як правило, задіюються ручні методи роботи, механізація виробництва незначна, як і перелік використовуваного оснащення.
Особливість серійного полягає в періодичному випуску рідкісних або популярних заготовок. Розмір партії може бути як незначним, так і досить великим. Застосовуються різні методи створення форм. Техніка та діяльність ливарного цеху також дуже варіативні.
Масовому типу властивий безперервний випуск будь-якої номенклатури відливок у значних обсягах. Часто цей варіант можна спостерігати в дії на авто- і тракторних підприємствах. Важливі вимоги до обладнання: інноваційність та високопродуктивність.
Яка сировинна база може бути задіяна? Це і окремі технічно чисті чорні й кольорові метали (залізо, сталь, сірий і високоміцний чавун, мідь, латунь, бронза, нікель, алюміній, магній, титан, цинк, свинець і навіть срібло, золото, платина), і їх сплави. Сплави, до речі, як можуть складатися з декількох металів, так і бути поєднанням метал + неметал. З популярних неметалічних компонентів: вуглець, сірка, фосфор і бор. Також не виняток – наявність домішок металевої і неметалевої природи, хоча в більшості випадків їх присутність небажана.
Загалом, відливки можна створювати з будь-якого металу, але кожному з них властиві свої ливарні особливості. Наприклад, різною є рідкоплинність – здатність максимально заповнювати форму, не залежно від її конфігурації. На ливарні характеристики впливають, передусім, хімічний склад і структура робочого матеріалу. Не можна не враховувати тут і температурний режим плавлення: чим він нижчий, тим лиття здійснюється легше.
Вибрати сировину, яка якнайкраще підійде для тих чи інших деталей, часто буває складно, адже врахувати всі нюанси практично неможливо. Однак, якщо добре розбиратися у властивостях металів, досягти позитивного результату буде набагато легше.
Що потрібно знати про властивості матеріалів, які застосовуються для лиття? По-перше, те, що при виготовленні простіших виробів до металів/сплавів висуваються не надто високі вимоги. Якщо необхідно створювати вироби з тонкими стінками, складними формами, дуже великих розмірів, та ще й дефекти небажані, то властивості сировини (висока рідкоплинність, мала усадка, незначні тенденції до утворення тріщин, схильність поглинати і формувати газові раковини, пористість та ін.) повинні бути враховані максимально.
Всі властивості металів поділяються на 4 групи:
- Фізичні (густина, t плавлення, тепло- та електропровідність, а також теплове розширення). Виявляються там, де не спостерігаються трансформації хімічного складу речовини.
- Механічні (твердість, міцність, в’язкість, пружність і пластичність). Обумовлюють здатність металу, а точніше відливки, виготовленої з нього, витримувати різного роду навантаження або проявляти опір до стирання в процесі експлуатації.
- Технологічні. Визначають, як будуть реагувати метали на різні методи обробки. До таких властивостей належать гнучкість і зварюваність, рідкоплинність і прожарювання, а також оброблюваність шляхом різання.
- Хімічні. Пояснюють відношення (здатність до опору) металів до хімічного впливу різних середовищ. Це, перш за все, стійкість до окислення та корозійного впливу.
Як визначити стан відливки і виявити дефекти? Зовнішні недоліки можна виявити шляхом огляду після вилучення деталі з форми і її очищення. Для внутрішніх необхідно задіяти або радіографічну, або ультразвукову дефектоскопію. Перша діє за допомогою рентгенівського або гамма-випромінювання і, таким чином, дозволяє визначити параметри й глибину перебування дефекту. Друга працює за іншим принципом: ультразвук потрапляє всередину відливки і відбивається при досягненні недоліку. Інтенсивність такого відбиття і дає інформацію про розмір та глибину дефекту.
Для виявлення тріщин можуть бути застосовані: люмінесцентний контроль, магнітна/кольорова дефектоскопія.
Хімія для ливарного виробництва
Сьогодні жодна сфера промисловості не обходиться без застосування хімічних речовин, ливарне виробництво – не виняток. Тут без хімії не обійтися, оскільки різні матеріали сприяють виконанню широкого спектру виробничих і функціональних завдань: досягненню точності заготовок, забезпеченню високої якості поверхні, легкому їх відокремленню від форм, підвищенню продуктивності, стабільності збереження форм і т.д. Розберімося в цьому питанні на прикладі й розглянемо кілька важливих у зазначеному сегменті промисловості хімічних компонентів.
Рідке скло. Застосовується, головним чином, як сполучник у формах і стрижнях для лиття, якщо робота ведеться з разовими формами (одиничне і дрібносерійне виготовлення). Також може бути задіяне при створенні антипригарних фарб і для лиття за моделями, що виплавляються. Використання рідкого скла в литті доцільно не тільки через його функціоналізм, а й з огляду на відсутність токсичного впливу, доступність та можливість досягати необхідних технологічних властивостей форм і стрижнів для лиття. Головне достоїнство рідкоскляної суміші полягає в зміцненні її стикування з оснащенням при кімнатній t.
Рідке скло – це водний розчин лужних силікатів. Якщо беруться натрієві силікати, то таке скло іменується натрієвим, якщо калієві – калієвим. Перше в литті більш поширене, оскільки ціна і дефіцит його нижчі, порівняно з другим.
Оцінка рідкого скла відбувається за модулем і густиною. Модуль, як правило, становить 2-3,1. Варто враховувати, що чим вищим є модуль, тим більша і полімеризація, і темпи затвердіння. Так високий модуль небажаний: через нього живучість суміші може бути зменшеною, міцність буде прискорено наростати в початковий період, але через якийсь час почне знижуватися. Якщо виникне потреба знизити модуль рідкого скла, використовуйте добавку натрій гідроксид.
Вибір параметрів рідкого скла залежить від формувальних сумішей:
- для рідкорухомих і самотвердних краще підійде високомодульне рідке скло з модулем 2,7-3 і більше, густиною 1400-1420 кг/м3;
- для стержневих сумішей із затвердінням за допомогою вуглекислого газу – з модулем 2,5-2,7 і густиною 1480-1520 кг/м3;
- для формувальних типу ФБС – з модулем 2,15-2,3, питомою вагою 1480-1520 кг/м3.
Каніфоль. Це крихкий, схожий на скло матеріал, що складається зі смоляних кислот і їх ізомерів. У ливарній справі виступає зв’язкою, що підвищує міцність. Також допомагає зменшити витрати рослинної олії. У модельних складах застосовується, зазвичай, соснова каніфоль 1-го і 2-го сортів і не самостійно, а разом з парафіном, церезином або іншими матеріалами з подібними властивостями.
Борна кислота. Ще одна зв’язка, що застосовується при кислому футеруванні печей. Крім того, захищає струмені розплавлених магнієвих сплавів від окислення.
Полівініловий спирт. Це розчинний у воді полімер зі склеювальною здатністю. Компонент сполучного, який задіюється при литті за виплавлюваними моделями. Дозволяє вирішити таку проблему, як мала міцність оболонкової форми. Крім того, поліпшує якість форми і термін придатності робочого матеріалу.
Парафін. Пластична недорога і недефіцитна суміш алканів. Застосовується для виготовлення ливарних моделей дуже часто. При цьому можуть бути використані різні види цього матеріалу: очищений технічний, високоплавкий з незначним вмістом олій (для підвищення стійкості до тепла та міцності), сірниковий (для надання підвищеної пластичності). Але оскільки у парафіну поряд із плюсами є й мінуси (крихкість, мала міцність, схильність до спінення й формування усадочних раковин, розм’якшення при t приблизно 30 °С), його переважно задіюють спільно з іншими матеріалами.
Церезин. Вуглеводнева суміш метанового ряду. Цьому матеріалу властиві збільшені пластичність та стійкість до тепла. Він, у порівнянні з парафіном, має підвищену t початку розм’якшення, меншу схильність до деформацій. Але, разом з тим, йому притаманні і висока лінійна усадка (до 1,1 %), незначні міцність й твердість. У ливарній галузі найбільш часто використовують більш тугоплавкий церезин синтетичної природи.
Стеарин. Є сукупністю твердих жирних кислот, основна з яких – стеаринова кислота. В литті задіюють зазвичай дистильований стеарин 1-го і 2-го сортів. Через певні недоліки (поява поверхневих дефектів на відливках, омилення при виплавлянні в гарячій воді, досить велика вартість та дефіцитність) його вважають за краще замінювати сумішами парафін + церезин або іншими.
Карбамід. Кристалічна маса, добре розчинна у воді. Цей реактив примітний при введенні в ливарні матеріали таким: плавлення при t 129-134 °С, значна рідкоплинність у розплавленому вигляді, а відтак і добре заповнення формених порожнин без використання тиску. Сечовина оперативно остигає в прес-формі, формуючи міцну і точну (завдяки невеликій усадці) модель, поверхня якої виходить гладкою. Дуже цінно те, що ця сполука нагріваючись не має стадії розм’якшення, тому унеможливлена деформація карбамідових стрижнів при t до 100 °С.
Для тих чи інших завдань у ливарній справі можуть бути застосовані і такі хімічні речовини, як: селітра кальцієва, етилсилікат, хлорид барію, поташ, фторид натрію, нітрат натрію і нітрат калію, полістирол, поліетилен, етилцелюлоза, уротропін та інші.
Реактиви ливарного виробництва
Важлива частина ливарного виробництва – реактиви. Що і для чого може знадобитися, залежить від оброблюваного металу/сплаву і, безпосередньо, від способу лиття. Як правило, хімічними реагентами виступають метали (титан, ванадій, цирконій та ін.) і неметали (бор, вуглець, вуглецевий кальцій, ціанамід кальцію...). При роботі з чорними металами можуть знадобитися соляна, сірчана, фосфорна і плавикова кислоти. Для обробки відливок з чавуну і кольорових металів способом фасонного лиття із задіянням ХТС беруть газоподібні реагенти. Якщо роботи ведуться з дорогоцінними металами, то тут не обійтися, наприклад, без хлорного золота для випробування відливок.
Пам’ятайте: найкращі реактиви для лиття – це хімічно чисті реактиви. При їх закупівлі необхідно проконсультуватися з виробником/постачальником, уточнивши всі потрібні питання.
Хімія для лиття металів – дуже важливий учасник виробничого процесу. Вона не тільки впливає на роботу, але й в певних випадках визначає якість кінцевого продукту, його властивості, практичність, довговічність тощо.
Щоб вибір хімічних речовин і реактивів не став для вас проблемою і не приніс зайвих труднощів, зверніться до наших фахівців. Розповімо все, що потрібно знати про ці матеріали для досягнення максимально бажаного результату при застосуванні, і допоможемо з поставками потрібних хімікатів!